DAKOTA inspection system, developed by the company GIPS vision, has been created for foam plants and most specifically for those manufacturing automotive seating.
It can inspect several types of components (or inserts) inside of a mold before foam injection.
It uses two 3D profile cameras to inspect both the tank or bowl and the lid directly on line, on-the-fly.
Benefits
- Prevents bad product
- Lowers scrap rate
- Monitors & controls process
- Improves productivity
- Reduces customer’s returns / claims
- Saves material (foam) costs
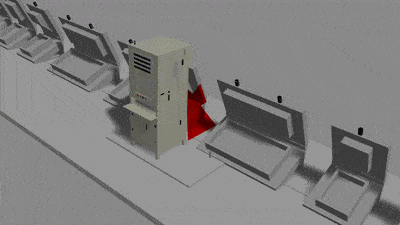
Advantage of 3D
- Z- Measurement
- No lighting problem
- Independent of mold appearance (aging, dirt, background color ...)
DAKOTA 3D Ressources
In DAKOTA 3D Downloads area you will find all the resources, instructions and technical features you need. A FAQ is also available for your most frequent questions.
3D machine vision-based component inspection
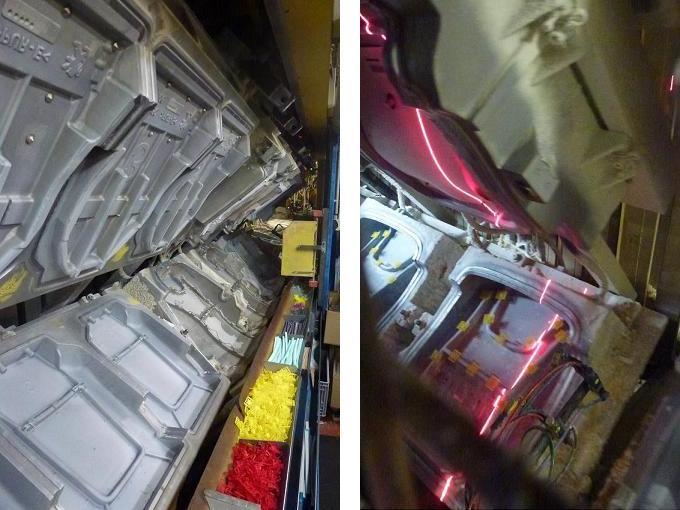
- On-the-fly mold control before injection
- Simultaneous inspection of bowl and lid
- 100% of the molds are checked 24 hours a day
- Up to 999 check points per mold
- 999 different mold references
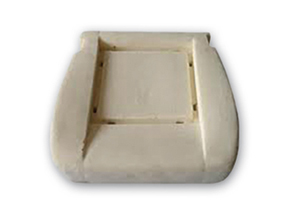
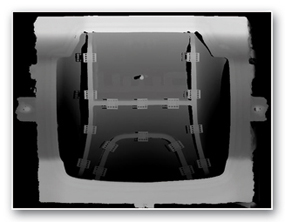
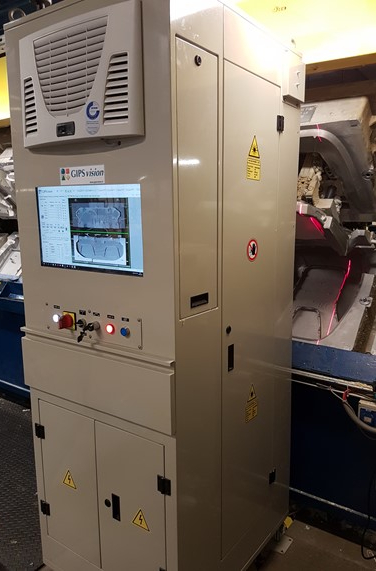
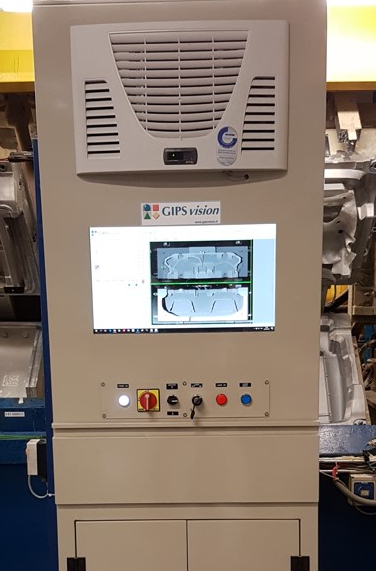
3D by triangulation
Two 3D modules
- High-performance camera, for accurate three-dimensional
measurements (2000 pixels, 1000 profiles/s) - Laser class 3B
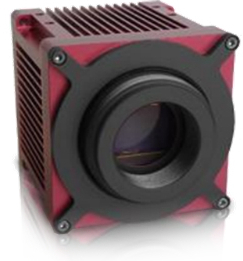
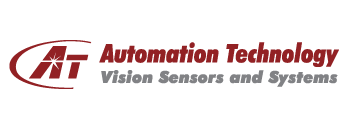
High speed 3D-profile camera
Dedicated software
- Fully configurable controls by intuitive graphical HMI
- Inspection tools: profile, shape, surface, texture, height, position, etc...
- Communication with line supervision (Profibus, Profinet, OPC, TCP-IP....)
- Recording statistics by team
- Production log
- Immediate and delayed display
Immediate and/or deffered display
Dakota communicates with line supervision through field bus(Profibus, Profinet, TCP/IP OPC...)
Recording statistics per shift Logbook.
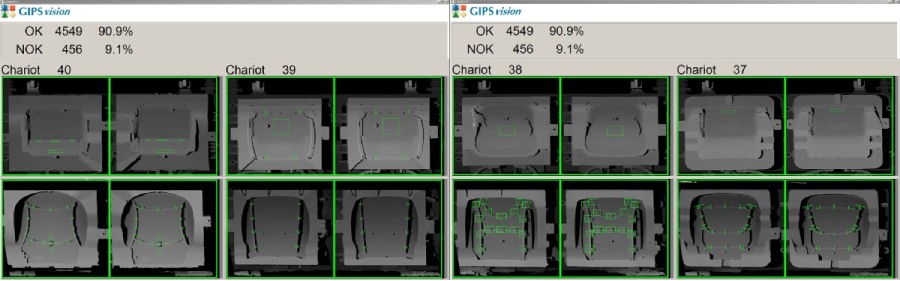
Suitable for all types of components




















Different types of inserts in molds before injection
Production statistics
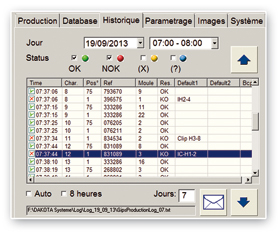
Performances
- Resolution < 500μm in X, Y, and Z
- Field width: 800mm
- Depth of field: 250mm
- Variable product length
- Speed > 15m/min
Cabinet enclosure 

Support for bowl & lid camera modulesLaser protections, PC and user panel
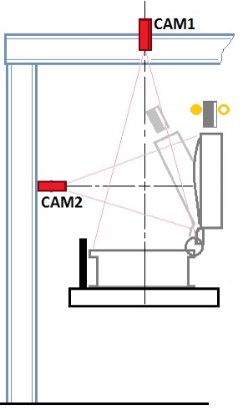
DAKOTA inspection system, developed by the company GIPS vision, has been created for foam plants and most specifically for those manufacturing automotive seating.
It can inspect several types of components (or inserts) inside of a mold before foam injection.
It uses two 3D profile cameras to inspect both the tank or bowl and the lid directly on line, on-the-fly.
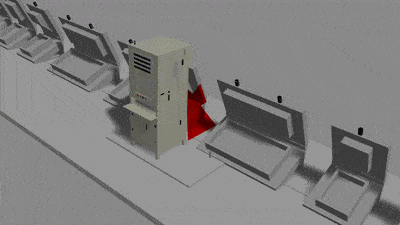
DAKOTA 3D Ressources
In DAKOTA 3D Downloads area you will find all the resources, instructions and technical features you need. A FAQ is also available for your most frequent questions.
The three major advantages of the Dakota system are:
- Avoidance of customer complains for incomplete products.
- Reduction of material loss (foam injection only when needed).
- Monitoring the damage, wear or condition of the mold.
3D machine vision-based component inspection
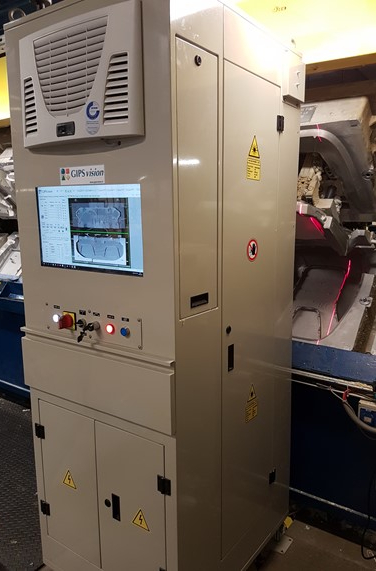
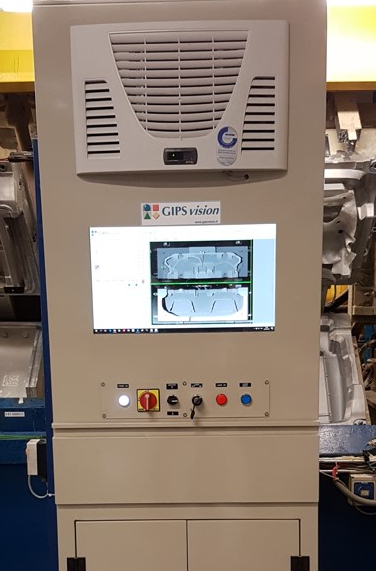
- On-the-fly mold inspection before injection
- Simultaneous inspection of bowl and lid
- Up to 999 check points per mold
- Up to 999 different mold references
- 100% systematic inspection 24/7
- Operating at production rate ~1000 parts/h
- and at line speed ~15m/min
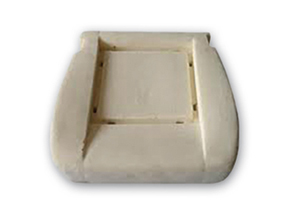
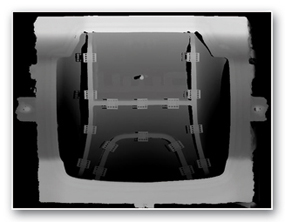
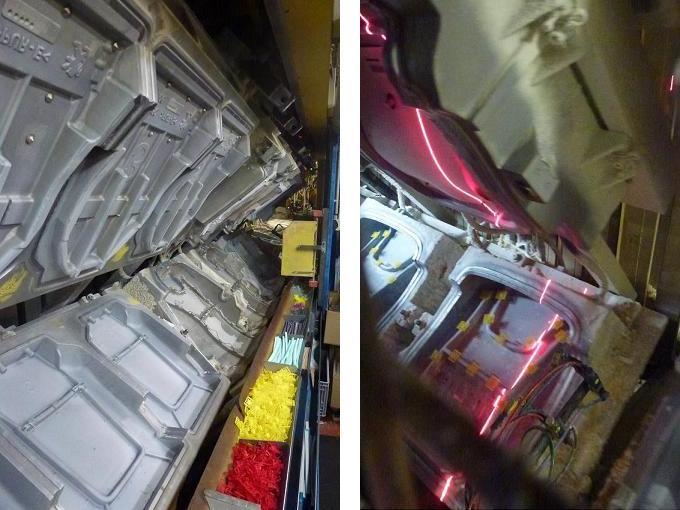
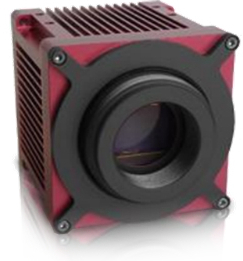
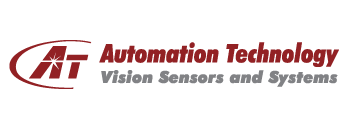
High speed 3D-profile camera
Two modules 3D Camera+laser
High performance cameras, 2000 pixels, 1000 profiles/s
+ Class III laser, on non-deformable base plate
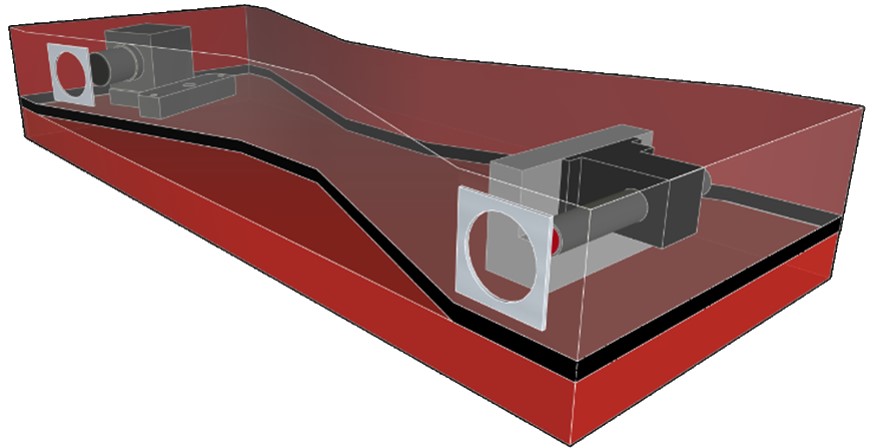
Dedicated software
Multi-thread Pc-based application Fully trainablecheck points through user-friend intuitive GUI
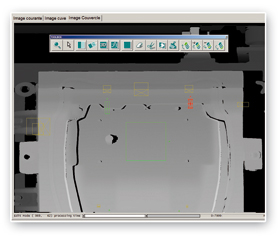
Immediate and/or deffered display
Dakota communicates with line supervision through field bus(Profibus, Profinet, TCP/IP OPC...)
Recording statistics per shift Logbook.
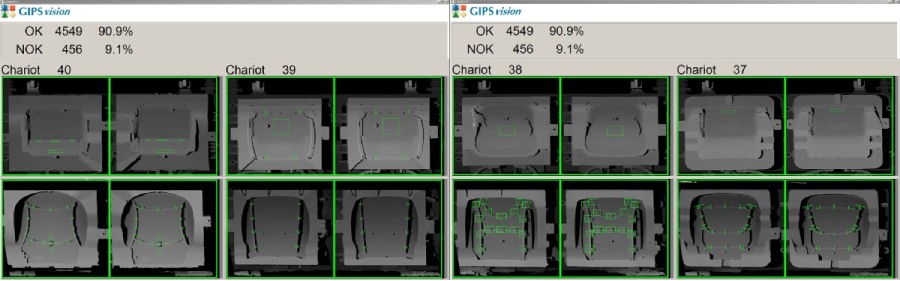
Suitable for all types of components




















Production statistics
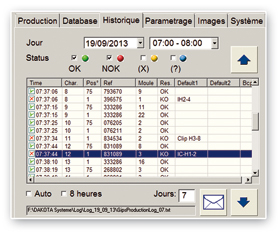
Cabinet enclosure 

Support for bowl & lid camera modulesLaser protections, PC and user panel
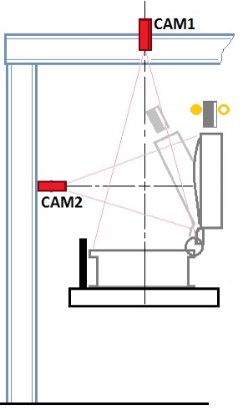
Performances
Field width: 800mmDepth-of-field: 250mm
X&Y resolution: 500µm
Products length: 1700mm
Installed on line edge
on racetrack or turn table
Line speed : up to 14m/min
Rate: 1 to 6 mold per carrier
Database up to 999 references